РБК-Аналитика: Основные проблемы и тренды импортозамещения в Башкирии
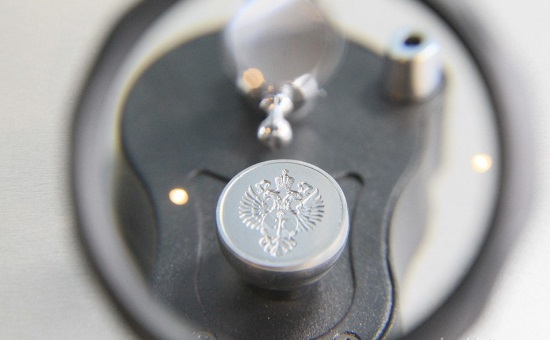
Афоризм «настоящая любовь похожа на привидение: все о ней говорят, но мало кто ее видел», отчасти можно применить и к импортозамещению. Это понятие, часто звучащее в речах чиновников, не измеряется какими-либо интегральными показателями и в комплексе не исследуется статистикой. Более того, оно разнородно: если для сельского хозяйства тренд на импортозамещение означает, по большей части, просто рост объемов продукции, то для промышленности это более сложные явления, часто связанные с освоением новых сфер и перестроением логистических, технологических цепочек.
Например, начальник отдела физико-химических исследований уфимского Института нефтехимпереработки Станислав Корчевский, рассказывая о текущем исследовании с импортозамещающей перспективой – покрытии, изолирующем от электромагнитного излучения, – говорит: «Мы выяснили, что немцы используют здесь многослойные графены. Технологией их производства у нас владеет только одна фирма в Подмосковье, сейчас мы изучаем образцы, которые они прислали. Если мы сможем наладить производство этой краски, то простимулируем их производство, а это, в свою очередь, перспективы для целой отрасли – электроника, сфера интересов «Роснано» и т.д.». Таким образом, одно новое производство в Башкирии косвенно может изменить структуру производства в других сферах и других регионах, и вряд ли статистика сможет комплексно посчитать его эффект.
Две отрасли плюс оборонка
В промышленности власти региона расставляют приоритеты импортозамещения следующим образом. На первом месте – всё, что связано с углеводородами (добыча и переработка нефти) и химией. В начале года министр промышленности и инновационной политики Башкирии Алексей Карпухин рассказал РБК-Уфа, что в некоторых областях нефтедобычи импортозависимость достигает 80-90%, по нефтехимии она оценивается в 20%.
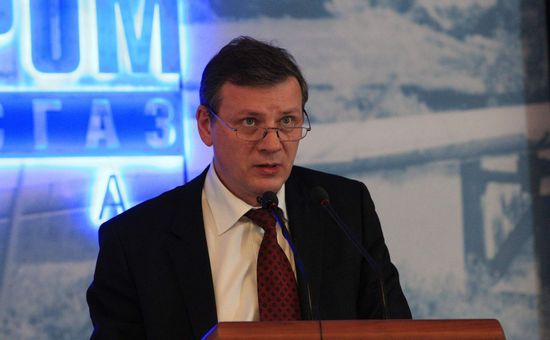
Министр оптимистично оценил компетенции региона в замещении импорта в нефтегазовом инжиниринге: по его словам, здесь «мы можем закрыть порядка 90% потребностей». Вторая сфера приложения усилий властей – машиностроение. Импортозамещение в ней власти региона оценивают как «крайне тяжелый» процесс.
Отдельно можно говорить об оборонном комплексе (его доля в отгруженной продукции региона менее 10%). По оценке Алексея Карпухина, «оборонка поспокойнее, здесь импортозамещение идет проще, чем на свободном рынке», но это компенсируется бóльшим количеством сертификаций: «Если ваша продукция связана с тем, что летает, то это все летные испытания. Значит, с начала вашей работы до того момента, как будет поставлен агрегат, пройдет около трех лет. Это иные регламенты».
Можно добавить: и иные механизмы. Как правило, в оборонной промышленности речь идет не о плавном выводе дорогостоящих импортных сегментов из цепочки, а о ее полном перестроении в авральном порядке: всё, что связано с вооруженными силами, в первую очередь попадает под санкции. Например, уфимская «Гидравлика» (холдинг «Технодинамика» «Ростеха») сейчас столкнулась с необходимостью освоить «очень большую» номенклатуру агрегатов, которые раньше производились на Украине. Гендиректор предприятия Сергей Денисов назвал эту ситуацию «непростой темой, которая осложняется жесткими сроками, тем, что документация не самая актуальная и т.д., но другого пути у нас нет». К решению проблемы срочно подключили уфимский Институт сверхпластичности металлов РАН. Добавим, что это происходит в непростой момент для уфимской оборонки: буквально несколько дней назад было объявлено, что «Гидравлика» и УППО (оба входят в «Ростех») вынуждены перевести на неполный рабочий день более 850 человек. Причиной названо снижение объемов производства.
Метод Шерлока Холмса
Как рассказали РБК-Уфа чиновники, курирующие тему импортозамещения, многое приходится делать «в ручном режиме», работа в этом направлении началась два года назад. Бывший вице-премьер Дмитрий Шаронов (ушел в отставку на этой неделе, когда материал готовился к публикации. – РБК-Уфа) называет несколько национальных корпораций, для которых Башкирия устраивала презентации инновационных проектов, и особо выделяет «Газпром».
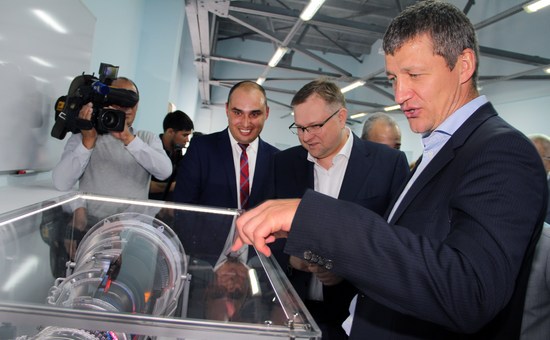
«Важно сломать стереотипы компании-потребителя. У «Газпрома» это получается лучше, видимо, больше выстроена иерархия, жестче кампания сверху в пользу импортозамещения». По оценке минпрома, количество заказов «Газпрома» на предприятях Башкирии выросло за два года на 20%, а средняя сумма заказов – на 40%. Среди производителей-партнеров корпорации Дмитрий Шаронов особо выделяет октябрьскую «ОЗНУ» (производитель нефтегазового оборудования), удвоившую объемы производства за год. В целом, по его оценке, количество «профильных» контрактов в сфере импортозамещения растет за год в полтора раза.
В области нефтехимии флагманом в регионе является государственный Институт нефтехимпереработки (в начале года включен в план приватизации). На его базе был создан центр прототипирования, получивший оборудования на 1 млрд рублей из федерального бюджета. Как рассказал РБК-Уфа директор института Эльшад Теляшев, «заимствование опыта – самый обычный путь. Мы не копируем, как китайцы, а изучаем образцы, делаем шаги вперед и создаем отечественные аналоги, двигаем науку дальше».
.
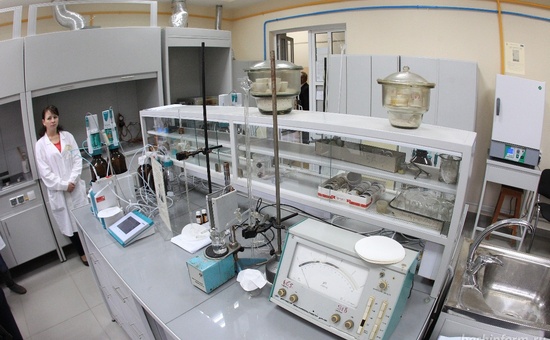
Более 70 лабораторий института «расшифровывают» образцы. Специалисты института говорят, что это законно, и называют процедуру «обратным инжинирингом». «Те объекты, с которыми мы работаем, наиболее успешны на рынке, – говорит Эльшад Теляшев. – Это сложные объекты, иначе они бы не были успешны. Люди потратили годы, а мы их за месяцы “раскидываем”». Он приводит примеры, когда «расшифровать полимер было трудно, производитель ввел туда какие-то экранирующие метки, чтобы мы не могли сделать спектральный анализ», но сохранить компонент в тайне это не помогло. Начальник физико-химического отдела Станислав Корчевский сравнивает работу коллег с работой Шерлока Холмса и называет метод «химической дедукцией»: «Иногда мы не понимаем ключевой элемент: вроде, всё собираем, а нужного эффекта достичь не можем. Потом мозговым штурмом догадываемся – какого элемента нам не хватает».
Директор института приводит некоторые примеры успешных импортозамещающих проектов последнего времени. Так, по заданию УМПО институт «разобрал» и за 4 месяца воссоздал на отечественных компонентах порошок для 3D принтера. Для минобороны за 3 месяца – полимерную добавку для укрепления грунтовых дорог, которую применяют для временных аэродромов и раньше получали по линии совета «Россия – НАТО». За два месяца, что в институте называют рекордным сроком, удалось сделать мастику для крепления каучука на бетон по заказу УЗЭМИК – по немецкому образцу: завод был вынужден закупать ее в Германии. Технология используется при строительстве метро. Для Белорецкого металлургического комбината институт определил основные компоненты полимерной оболочки, которая не рассыпается от нагрузок и температур и может применяться для производства многопрядных стальных канатов диаметром до 90 мм, которые раньше производились только за границей. Комбинат получил заем минпромторга РФ в 255 млн рублей на это импортозамещающее производство.
Проблема № 1: Не хотят покупать
Вопрос о том, насколько импортозамещение востребовано не госполитикой, а реальными субъектами экономики, стоит довольно остро. «Если мы смотрим в программу минпрома России о необходимости того или иного оборудования, то я не вижу там потребителя. Кому именно это нужно? – спрашивает Дмитрий Шаронов. – Куда я должен со своей инновацией пойти?». По его оценке, документы носят несколько «внутриведомственный» характер. «Есть проблемы даже с нашими компаниями [в Башкирии], которые не идут на контакт, выдумывают разные предлоги, но продолжают покупать импорт. У кого-то логистика уже выстроена, у кого-то долгосрочные контракты, а кто-то не очень верит, что наш производитель может конкурировать по качеству. Ну вот так мы ментально воспитаны, что импорт лучше. Исторически это связано с некоторой необязательностью, срывом сроков, увеличением цены уже заказанной продукции. Огромный объем бюджета уходит на Запад по тем технологиям, которые у нас есть и работают».
Бывший вице-премьер приводит пример с одной из крупных корпораций, которая «недавно организовала конкурс на создание технологии. Общий бюджет был около 10 млн рублей, а за готовую технологию компания платила на Запад десятки миллионов долларов. Это было похоже на то, как будто хотели накормить одним бутербродом целый вагон людей. Естественно, за такие деньги не нашлось желающих делать такую работу».
Часто заказчик ведет себя ненадежно даже в чисто коммерческом секторе. В институте нефтехимперерабоки рассказали о созданном ими российском аналоге шведского кинетического песка: «Вся наша родная страна – по линии минобразования, для школ, детских садов – закупает его за валюту. Российская компания заказала нам его аналог. Надо сказать, интернет кишит рецептами, и ни один не правильный. Там есть элемент, который целиком определяет поведение всей структуры. Но мы расшифровали: полимер оказался из лактозы. За три месяца мы изготовили свой продукт, себестоимость которого на порядок ниже. Но, к сожалению, заказчик не стал его производить. Мы готовы передать его любой другой компании».
На вопрос РБК-Уфа Эльшад Теляшев пояснил, что такие ситуации периодически возникают: «Жалко, конечно, но так бывает. Но через какое-то время мы можем предложить результат своей работы другой компании, потому что авторское право за нами, причем, мы хотим получать процент, когда продукт начнет производиться и продаваться».
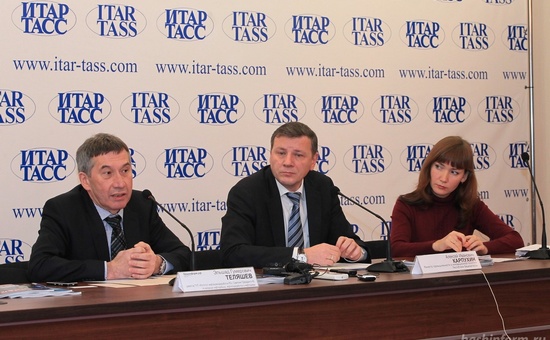
Проблема № 2: Не хотят продавать
По словам собеседников РБК-Уфа, производители из Башкирии не слишком охотно входят в импортозамещающие программы, потому что работа с крупными корпорациями грозит большими сложностями: сертификацией, испытаниями продукции, аудитом компании на предмет ее жизнеспособности... Рассказывая о взаимодействии с «Газпромом», Алексей Карпухин признается, что «участие в их импортозамещающих программах не гарантирует предприятию продаж». «Чтобы вы участвовали в торгах, вам нужно получить сертификат «Газпрома». Приходит компания «Новотек» и говорит: нас не интересует сертификат «Газпрома», нам нужен другой сертификат. Сделайте его, если хотите участвовать в тендерах. Только участвовать! Предприниматель думает: я сейчас вложу в сертификацию 10 млн, а гарантии, что выиграю тендер, нет».
При работе на корпорации ситуацию осложняет и колоссальный «кассовый разрыв», достигающий сейчас полутора лет. «Платят через 3-4 месяца после пуска оборудования. Это за свой счет сначала проект закажи, потом металл, энергетика, люди, транспорт, монтаж, пуско-наладка...»
Эльшад Теляшев жалуется, что корпорации-заказчики «все перешли на работу без аванса, все они платят после подписания акта, а это отдельная история, у них отсрочка 90 дней, а у некоторых и 180. Если брать кредит в банке, то полтора года – это, в лучшем случае, переплата 30%. Значит, я должен заложить прибыль в 30%, чтобы хотя бы выйти в ноль. Кто себе может это позволить? Никто! И все находятся в таком положении, и машиностроители, и нефтесервис...»
Проблема № 3: Базовые достижения Запада уже не догнать?
Разговоры о многих проектах в области импортозамещения упираются в то, что тот или иной базовый элемент невозможно сегодня произвести в России. Речь идет, например, о видах биоразлагаемых пластиков. Кстати, в работе по их созданию участвует, в партнерстве с институтом генетики РАН, инновационная площадка, созданная в Башкирии: это региональный центр инжениринга в области биотехнологий. Подробнее о нем и о других центрах прототипирования, созданных властями Башкирии в последние два года, можно будет прочитать в материале РБК-Уфа в ближайшие дни.
«К сожалению, большая часть компонентов для производства аналога выпускается не в России», – говорит Эльшад Теляшев об очередной институтской новинке, но за этими словами следует: «Но даже если мы закупаем сырье за границей, это все равно на порядок дешевле». Он показывает термоусадочный полимер, который заменяет гипс при травмах. То же говорится о гелевом полимере, который также может использоваться в медицине – в матрасах для лежачих больных: «Базовый элемент у нас не выпускается, это продвинутый трехблочный полимер, который нам придется покупать». Эти же слова звучат, когда специалист рассказывает о секретах испанского мягкого пластилина, исследование которого заказано российским производителем – заводом «Луч»: «На упаковке указано, что он собран из натуральных ингредиентов. Правда, понятие «натуральности» здесь очень скользкое. Заказчики очень удивились, когда прочли наше исследование, потому что ожидали, что он состоит чуть ли не из пищевых продуктов. Нет: состав вполне классический, но есть одна изюминка. Этот мономер выпускается только одной компанией мира». Правда, Станислав Корчевский добавляет, что «мы поняли, чего нам не хватает для его производства, и сейчас ждем. Если получится, мы планируем использовать его по аналогии с пластилином, например, в битумах, чтобы бороться с колейностью».
Иногда делать полный аналог, то есть заменять все составляющие импортного продукта или технологии, слишком долго и дорого, а иногда в этом просто нет смысла. Еще в одном «штабе импортозамещения» – радиоэлектронном кластере Башкирии – Виктор Эриванцев, исполнительный директор проекта «Finch» и резидент кластера, рассказал о своем проекте. Он признается, что электронику для плат фирма покупает, в основном, в Китае, несмотря на то, что этажом ниже новейшая техника центра работает с похожими платами. «С импортозамещением у нас в этом смысле тяжело, – поясняет он. – В Китае это называется «рассыпуха», то есть очень дешевые детали, которые они производят миллионами в месяц. Если в России делать их производство, это будет дороже довольно долгое время».
Экономика должна быть экономной
Впрочем, перспективы импортозамещения открываются там, где у Запада нет причин форсировать работу над технологиями. Специалист радиоэлектронного кластера Олег Целишев рассказывает о новой технологии нанесения на электронные платы защитного лака и демонстрирует собранный здесь аппарат. Технология нужна для аппаратуры, используемой в агрессивных средах.
Говоря о достоинствах аппарата по сравнению с импортными аналогами, он сообщает, что «никто в мире еще не решил проблему автоматического контроля качества в процессе нанесения лака». На вопрос, что же остановило американских и европейских производителей, он признается, что «для них не так остро стоит вопрос замены платы, как для наших потребителей»: чисто по финансовым соображениям. По его словам, в Уфе «не стали придумывать велосипед, взяли зарубежную технологию и немного ее модернизировали». В частности, добавили компонент, который позволяет снимать лак и заново покрывать плату в случае брака. «На Западе, если плату покрыли неправильно, ее либо выкидывают, либо отправляют на переработку». Российский производитель не может позволить себе такой расточительности.
Так что необходимость экономить все еще открывает перед российской наукой и техникой широкие перспективы.
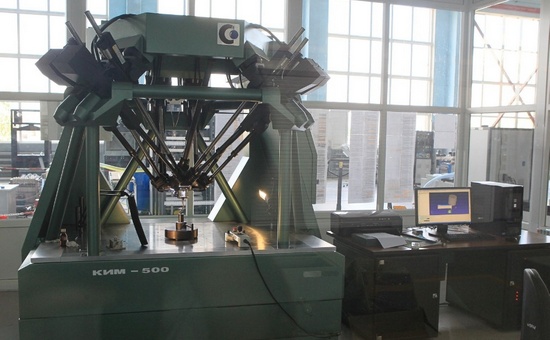
Немного статистики
В 2015 году объем импорта в Башкирию составил 0,5 млрд долларов США: это ровно половина от показателей 2014 года. 49% из всех ввозимых товаров составила продукция машиностроения, еще 36% – химические продукты, 8,8% – продукция металлургии, и только 2,6% – продовольствие. Понятно, что падение, в основном, связано со снижением покупательской способности, но в целом внешнеторговый оборот упал на 40%, то есть чуть менее радикально. Промежуточные данные 2016 года трудно оценивать объективно, потому что, как заявляют в региональном управлении таможни, объемы и структура экспорта-импорта сильно зависят от сезонности.
Индекс промышленного производства в Башкирии, по данным Росстата, продолжает расти: такую тенденцию показывают только половина регионов Поволжья, по России в целом этот показатель снижается. В 2016 году этот индекс составил в регионе 102% (по данным за 10 месяцев) в сравнении с аналогичным периодом прошлого года. При этом темпы рост все же плавно снижаются с 2010 года: тогда индекс составил 110%, а по итогам 2015 года он был оценен в 101%.
Согласно данным, озвученным в октябре на профильном совещании глав субъектов Приволжского федерального округа, в 2015 – 2016 годах специальные транши на импортозамещение получили 102 предприятия ПФО, ее сумма составила 8 млрд рублей.